Built for the grind:
Why electric mini-loaders are reshaping mining cleanup
Written by William Nicholls | July 15th 2025
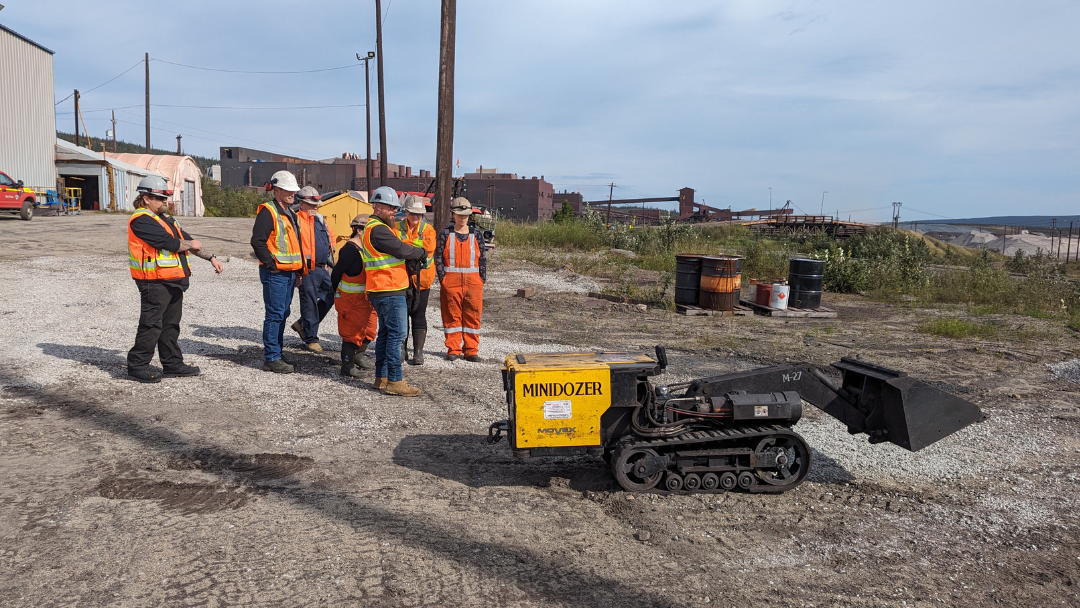
In a mid-sized mining operation in Australia, material cleanup had become a large-scale bottleneck. After every blast, a crew was sent in with a diesel mini-loader to push rubble out of the way and restore access. It was a routine that played out hundreds of times a year.
But the equipment, worn from constant exposure to hazardous conditions, started failing more often. One morning, it stopped halfway through clearing under a critical conveyor or access tunnel. The crew had to haul it out manually—costing them many hours of production and a couple hundreds of thousands of dollars in lost output and maintenance expenses.
It wasn’t an isolated incident. Over the next quarter, mechanical failures and unplanned servicing chewed through the operation’s margins. The mine manager had had it. He finally pulled the data: high maintenance costs, frequent downtimes, and growing safety concerns tied to having operators in unstable zones. That’s when he started to look for a more contemporary solution to an age-old material cleanup problem.
In mining jobs, where heat, pressure, and dust converge, material cleanup is never just a routine task. Material handling and clearing debris in mining often come down to equipment durability and performance. The conditions are unrelenting, and any weak point—a hydraulic leak, an overheating motor, or a snapped track—can bring production to a halt. For mining operations managers, every minute counts, and equipment downtime translates to real financial consequences.
As mines evolve to meet stricter safety standards and emission targets, the choice of material cleanup equipment is changing. Electric and ultra-compact mini-loaders, once seen as niche, “nice-to-have” tools, are becoming indispensable.
The toll of mining environments on equipment
Few industrial settings are brutal towards machinery like underground mines. The terrain alone is enough to wear down many conventional loaders. Jagged rock, uneven surfaces, and steep inclines subject equipment to continuous shocks and vibration. Structural components face relentless pressure, leading to fatigue cracks, loosened bolts, and increased danger of malfunction.
As everyone in the mining industry knows, mineral dust and rubble wreck underground gear. Fine particles infiltrate engines, motors, and electronics, clogging filters and choking components. Without advanced filtration and sealing, overheating and early component failure become inevitable.
High humidity and exposure to corrosive agents compound the problem. Moisture, combined with chemicals used in blasting or water ingress from underground sources, accelerates rust and degrades both metal and electronic systems. Over time, even protective coatings break down, exposing critical parts to damage.
Temperatures vary widely in mining, from northern Canada to the Middle East and Australia. Prolonged exposure to heat deteriorates lubricants, damages seals, and puts thermal stress on engines, batteries, and hydraulic systems. Meanwhile, heavy loads test the limits of hydraulic components and chassis. Every run boosts the possibility of overloading the equipment’s core assemblies.
Stretching (or skipping altogether) regular inspections and maintenance increases the possibility of a breakdown—and hundreds of thousands in downtime.
Old habits vs. new standards: Comparing diesel and electric mini-loaders
For decades, diesel-powered mini-loaders have been the standard in mining. Rugged, familiar, and relatively affordable upfront, they were the natural choice. However, their advantages have started to erode.
Diesel units demand constant maintenance: oil changes, fuel and air filter replacements, coolant checks, and engine servicing. Fuel injector cleaning and exhaust system upkeep are part of the routine, especially with tighter emissions regulations. In addition, their internal combustion engines, while powerful, suffer high wear on turbochargers and other moving components.
In contrast, electric mini-loaders eliminate many of these failure points. No combustion engine means fewer moving parts and less routine servicing. There are no oil changes, no radiator maintenance, and fewer lubrication needs overall. Maintenance is mainly reduced to battery state of health and basic mechanical checks, which drives down upkeep costs.
The cost difference grows with time. While diesel loaders may have a lower purchase price, their fuel needs fluctuate with market prices, and their engineering complexity leads to frequent repairs.
Electric machines, powered by rechargeable batteries, benefit from lower energy conversion losses and fewer parts susceptible to wear. Over a five- to ten-year lifecycle, the operational savings can be huge.
Reliability in harsh environments also tilts the scales. Electric loaders don’t require warm-up or cool-down cycles. They have no air intake systems to clog or exhaust components to rust or malfunction. The result? When equipment holds up, so does a mine’s throughput schedule.
Then there’s the worksite impact. Diesel engines produce emissions, heat, and noise—a triple threat in confined spaces. Ventilation requirements increase, both in scale and cost.
Electric loaders operate in near silence, with no emissions and less heat output. They reduce the need for forced ventilation, which can be a major expense.
Performance where it matters: The practical benefits of going electric
Mines leave little room to maneuver for material handling. With tight tunnels, conveyors, and narrow access points, bulky gear just slows things down. Electric mini-loaders are built for these spaces: they are ultra-compact, responsive, and easy to handle when inches matter.
Occupational safety is another area where electric systems gain ground. Remote-control capabilities are increasingly integrated into modern electric mini-loaders, allowing operators to work from a safe distance—away from waste piles, unstable ground, or blast areas.
Keeping personnel out of harm’s way not only reduces potential injuries but can also lower insurance premiums, cut down on incident-related shutdowns, and improve compliance with increasingly strict safety regulations.
For operations managers, it’s a safety upgrade that also makes financial sense.
Efficiency is easy to spot when material cleanup takes half the time. Manual removal burns through time and energy, while electric loaders move faster, stay consistent, and reduce the physical strain on crews. The result? Quicker turnarounds and smoother shifts.
Finally, there is the long-term financial perspective. Mines operating on tight margins cannot afford frequent equipment failures or costly downtimes. Electric mini-loaders, though higher in initial cost, offer stability in maintenance and energy expenses. Their reliability translates into uptime, and uptime is what drives profits.
A technology transition driven by necessity
The transition to electric mini-loaders in underground mining is a calculated response to the burden of material cleanup. When equipment must endure punishing conditions day after day, robustness isn’t optional. And as regulatory pressures grow and safety standards tighten, operations managers are reassessing what kind of material equipment belongs on their site.
Electric mini-loaders are proving they can withstand the grind—dust, heat, vibration, and all—while offering consistent performance and lower total cost of ownership. With mining equipment, failure is not an option. Sticking with outdated equipment isn’t a risk worth taking.
Tired of downtime and rising maintenance costs?
Discover how electric mini-loaders can keep your mining operation running safely and efficiently.